Kubota Fulfills Parts Promise To Customers Keeping Parts Available
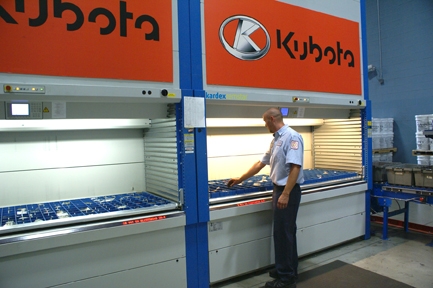
Kubota Fulfills Parts Promise To Customers Keeping Parts Available
Kubota Canada has been introducing groundbreaking tractor and utility vehicles for construction, commercial and residential use for 36 years. With an industry leading reputation for equipment that lasts; Kubota’s parts promise is what keeps customers coming back. Kubota is committed to keeping parts available for 20+ years; assuring the local Kubota dealer has quick access to the parts their customers need. That’s great news for Kubota customers, but presents quite a challenge for Kubota’s 60,000 square foot parts distribution center.
With 20+ years of legacy parts and additional inventory for new models introduced every year the parts inventory at Kubota’s part center in Markham, Ontario has steadily grown to over 78,000 SKUs. “Our parts promise to our customers presents a challenge as we have to inventory quite a few slow moving parts that are only picked a few times a year or in many cases not even once per year. But when a customer needs it, we have to be able to supply it,” says Doug Ward, Logistics Manager, “and the system we have in place allows us to do just that.”
Pick and Pass
Kubota’s parts center utilizes a pick and pass strategy with three picking zones. Six horizontal carousels from Kardex Remstar manage the fast moving SKUs; four Shuttle VLMs from Kardex Remstar house the medium moving SKUs and the slower moving SKUs are stored in hi bay shelving.
Horizontal Carousel Zone
The complete system was purchased and implemented in phases. In the first phase, Kubota purchased six horizontal carousels to replace a three story mezzanine in coordination with a building relocation. “With the horizontal carousels people are now picking parts ergonomically, there’s no more walking up and down the stairs to pick parts orders. Everything is on one floor and delivered right to the worker,” says Ward.
With little travel time to pick the part, picking productivity has also increased. In the mezzanine zone workers were picking an average of 20 lines per hour. “We couldn’t throw any more bodies into the mezzanine zone without people tripping over each other. With parts sales growing we needed to pick faster,” said Ward. Now, one person working in the horizontal carousel zone picks an average of 225 lines per hour while bagging and tagging. “We were able to increase our picking productivity by over 90% and only need one worker to manage the carousel zone,” said Ward.
The mezzanine at the old facility was three floors and occupied 9,000 square feet (3,000 square feet per floor). The horizontal carousels in the new facility required 71% less floor space. Including the workstation, picking area and the six 24 foot long horizontal carousels the picking zone occupies 2,600 square feet and the parts are all on one floor.
Shuttle VLM Zone
The second phase of the picking system was the Shuttle VLM zone. “We were out of space and considered a building expansion,” says Ward, “The Shuttle VLMs allowed us to actually reduce the footprint rather than a building expansion.”
Kubota started by installing two Shuttle VLMs to replace 2,400 sq feet of 18’ hi-bay shelving. Shortly after, two more Shuttle VLMs were installed to replace 1,200 sq feet of 24’ hi-bay shelving. With the workstation, picking area and four VLMs now occupying 620 square feet, Kubota was able to free up just under 3,000 square feet of floor space to increase parts capacity; an 83% floor space savings.
“Along with increased part capacity and improved ergonomics, picking productivity in the VLM zone has doubled,” says Ward. With only one worker in the zone and eliminating travel time to the part locations, picking productivity has increased by 50%.
The Way Of The Past
In the original system, all orders started at top of mezzanine shelving area. Workers picked the parts required for the order and carried the order down to the second floor to pick any parts required before traveling to the ground floor to finish picking from the mezzanine area. Once they had all the parts the needed from the mezzanine area they continued to the hi-bay shelving area to complete the order and then dropped it off at shipping.
New & Improved
The new system continues to use a pick and pass strategy, but has three picking zones. Kubota dealers place parts orders via the website. The host system sends the order to the system control software. All orders start in the horizontal carousel zone that manages the faster moving SKUs. The worker inducts up to eight orders into a batch. The system control software automatically selects the next eight orders, but the worker can manually pick specific orders if desired. Each order in the batch is assigned a tote and a location on the batch put station.
Orders are prioritized at order entry by the dealer when they place the order. Priority orders that must ship the same day are sent to the top of the list, all other orders are for stock and are picked in the order they are received.
When the batch is ready to be fulfilled, the six horizontal carousels spin to position for the first pick. Using pick to light technology the worker is directed to the carousel containing the first pick. The location to pick from is indicated with an arrow and the quantity to pick is displayed. The worker picks the specified quantity and turns to the batch station to distribute the parts among the orders as directed by the put lights. Once the first part picked is distributed among the eight orders, the worker continues to pick the next part from the carousel as directed by the pick lights. The carousel control software organizes the picks so that the next pick is always ready and the worker is rarely waiting. The worker picks round robin until all parts required from the horizontal carousel zone have been picked and placed into the orders on the batch station.
If order is complete it is routed directly to shipping. If the order requires further parts, it is routed to the VLM zone for further fulfillment. The Shuttle VLM zone works in a similar way to the horizontal carousel zone. The operator inducts up to eight orders at a time and picks round robin from the four VLMs. Each VLM presents the parts required and using pick to light technology directs the operator to the exact location to pick from and displays the quantity to be picked. Once the orders are fulfilled from the VLM zone they are sent to the hi bay shelving zone. If the order does not require any parts from the VLM zone it is routed directly from the horizontal carousel zone to the hi bay shelving zone.
Using a Raymond man-up order picker with a custom batch cart, the remaining parts required for the order are picked from the hi bay shelving zone containing the slower moving SKUs. The worker travels the hi bay shelving with a hand held RF gun directing them to the pick location. When the order is complete the worker is notified on the handheld RF gun and the operator delivers the completed orders to shipping.
Hot Picking
When an order needs to be fulfilled immediately it is flagged at order entry and given a status of “hot”. The order jumps to the top of the list; picked into a different color tote and routed through the picking process immediately.
Room for Growth
Part sales has grown steadily while labor requirements have only increased by 27%. “With the automation and process changes we’ve implemented, we’ve been able to manage 70% growth in the past 12 years with minimal increases to our labor force.” said Ward.
The parts center is ready for whatever new model Kubota dreams up next. “With inventory growing every year, the automated picking system we have in place has the capacity to sustain our growth for the next 5 – 8 years,” said Ward.
Kardex Remstar, LLC, a company of the Kardex Group is a leading provider of automated storage and retrieval systems for manufacturing, distribution, warehousing, offices and institutions. For information on automated storage and retrieval systems, call 800-639-5805 or visit www.KardexRemstar.com.