The Vertical Lift Module - The Most Flexible Storage System
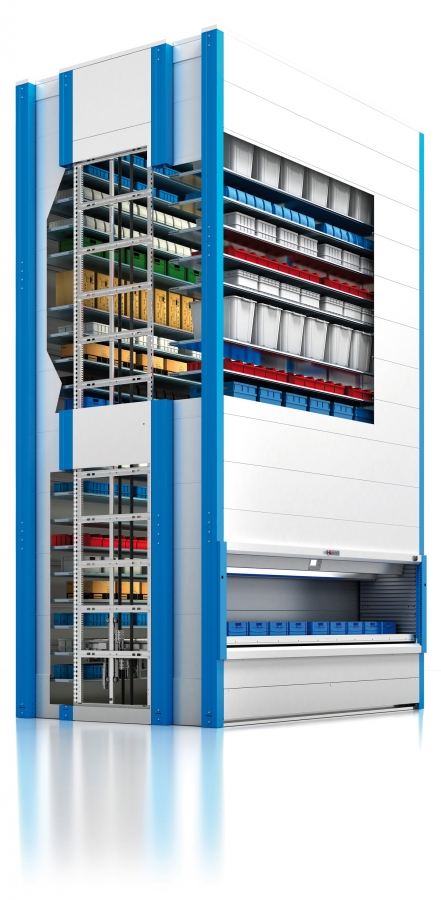
The Vertical Lift Module - The Most Flexible Storage System
With so many choices on the market today what makes one storage technology better than the other? In today’s economy, flexibility. With organizations constantly changing, growing and shrinking flexibility in storage system isn’t an option, it’s a requirement.
The vertical lift module (VLM) is the most flexible storage system on the market today. It can be altered and adapted as business processes change. A VLM is an enclosed system of vertically arranged trays, controls and an extraction platform that delivers goods to a workstation, but that’s not what makes it the most versatile storage system. There are five features of a Shuttle® VLM that make it the most flexible storage device around.
1. Modular Design- VLM’s have a modular design allowing the location, height, and configuration to be easily changed as an organizations business evolves. VLMs can be relocated throughout the facility or moved to a new facility altogether. Height modules can be added or removed post installation to change the unit’s height, always utilizing the vertical floor to ceiling space available to maximize storage density.
The VLM can be utilized in several different configurations, meeting a variety of needs within an organization. Stand-alone units can be strategically placed in manufacturing and assembly work zones allowing parts to be inventoried and accessed at the point of use. A group of VLMs can be configured into an picking zone to provide order fulfillment for manufacturing kits or parts distribution. Units can also be placed side-by-side and back-to-back for additional space savings. Unlike other storage systems, VLMs can be moved and reconfigured at anytime to meet changing needs.
2. Dynamic Tray Allocation- CubeStar® technology combines both hardware and controls using dynamic storage allocation to maximize the storage density within the unit. Upon put away, the height of each tray is measured to the nearest inch, allowing the VLM to determine the trays exact storage height requirement. The system determines the best position in the machine based on the least amount of spaced required.
This is ideal for organizations with materials that may vary in height. As the product height changes, the VLM automatically adjusts the storage requirements of the tray to always ensure every inch of space is utilized most efficiently. Other storage devices do not make this dynamic allocation for height and must store the box in a fixed space leaving unused space in the machine.
3. Multiple Access Openings – Unlike other storage units, the VLM can be equipped with several access points to link work zones together and maximize productivity. With multiple access openings in one unit, facilities can receive materials on one level and extract them on different work zone levels, eliminating the need to have to deliver materials from one floor to another. For example, workers on the third floor can access goods stored within the VLM by workers on the first floor, eliminating traveling up and down stairs all day.
VLMs can also be equipped with access points on the front and back of the unit, allowing departments located on the same floor to have immediate access to stored goods. Multiple pick windows can provide queuing and sequencing of parts, kits or completed orders for consolidation or shipping. Item returns can also be handled more efficiently with multiple pick windows since they can be received in one area and removed in other work zone for repackaging, quality checks, repair, or accumulation. The modular construction and rail panel design allows the number of pick windows, their size and location to be changed at any time.
4. Intelligent Tray Storage- The intelligent tray feature of the VLM improves the efficiency of a picking operation. The VLM automatically tracks the number of times specific trays are accessed by the operator. Trays accessed most frequently are stored closest to the VLM’s access opening for faster delivery, decreasing wait time and increasing operator productivity. The more the system is used, the more intelligent it becomes. For example, seasonal items are stored further away from the access opening during off season, but will be stored closer the more they are used as seasonal demand increases. The VLM is one of the only storage devices designed to adapt to an organizations picking needs.
5. Dual Tray Delivery- VLMs also allow for dual tray delivery to speed picking efficiencies. While an operator is working to retrieve a part from a tray currently in the access opening, the VLM extractor moves behind the closed shutter doors to pre-position the next tray required for picking. When the operator is finished with the current tray, the VLM delivers the next tray waiting behind the shutter doors before retrieving the current tray. This eliminates the operator wait time between picks. Pre-position picks keeps the VLM one step ahead of the operator, something that isn’t possible with other picking systems.
These five features make the Shuttle VLM a smart and flexible storage device that adapts as business changes. From simple storage needs to the most complex warehouse, the VLM can be customized to fit an organizations business needs today and in the future.
Kardex Remstar, LLC, a company of the Kardex Group is a leading provider of automated storage and retrieval systems for manufacturing, distribution, warehousing, offices and institutions. For information on automated storage and retrieval systems, call 800-639-5805 or visit www.KardexRemstar.com.