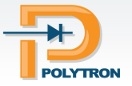
Share And Share Alike
Improve Business Workflow With SharePoint Tools You Already Own!
The ability to collaborate, share information and manage content from the plant floor to the C-suite may already be available if your facility uses Microsoft servers. However, putting the power of SharePoint to work takes more planning and preparation than simply booting up the software.
Leverage the tools you probably already have to increase efficiency.
Use of Microsoft SharePoint continues to increase as it is adopted by more corporate IT departments to provide company-wide infrastructure for collaboration, information sharing and content management. Global manufacturers are also learning the value of this tool for sharing contact lists and files and for streamlining manufacturing processes.
A global food manufacturer recently turned to Polytron to help it leverage the power of SharePoint to increase visibility and access its critical safety, downtime, quality and other operational data. The manufacturer had previously implemented paper-based, comprehensive workflow processes for handling incidents related to poor quality product, injury to plant personnel, safety violations and equipment/line downtime events.
Facing the drawbacks of paper records. This manufacturer’s standard operating practices had included paper-based workflows. These documents were updated and accessed by the various team members as incidents occurred. In addition to using paper to record information about the events, the process also included: notifying relevant plant personnel, investigating and collecting further information, checking to see if the same type of event had occurred previously, informing higher level management of more severe events.
Unfortunately, the paper-based system had several significant drawbacks. Only one person could work on the system at a time, causing inefficiencies and frustrations. There was also a chance that the master documents could be lost or misplaced – which did happen occasionally.
Success is more than going from paper to digital.
Adopting SharePoint would make a big difference for this manufacturer, but it would need to be more than simply converting paper processes to electronic ones. A conversion provides an ideal opportunity to update user requirements specifications (URS) as well as a method for streamlining processes. Polytron assisted the manufacturer in this crucial step, interviewing key stakeholders – both one-on-one and in teams – to develop an effective plan.
That’s because a workflow solution can touch nearly every portion of a plant, including quality, operations, plant management, IT and others Polytron assisted the manufacturer in this crucial step, interviewing key stakeholders – both one-on-one and in teams – to develop an effective plan. That’s because a workflow solution can touch nearly every portion of a plant, including quality, operations, plant management, IT and others.
Start by determining what success looks like for each stakeholder.
The key is uncovering what a successful implementation looks like from the perspective of each stakeholder, with all the information available and accessible in one place.
SharePoint can automate workflows and allow for multi-user and remote access. It delivers better visibility of the information and improves security through user password protection and tracking. The new process developed for this manufacturer consists of an automated, web-based system accessible from any computer within the facility. The system integrates with the manufacturer’s existing SharePoint sites, is automatically backed up and is relatively easy to modify as improvements to the workflows are identified.
Develop system based on workflows.
Polytron also used its technical expertise to document the plant’s workflows to track and eliminate anomalies. In conjunction with stakeholders at the facility, Polytron then developed the functionality of SharePoint Workflow System. Microsoft Office InfoPath, which the manufacturer already owned, proved useful for the design, distribution, filing and submission of electronic forms containing structured data.
Switching from a manual paper-based system to an automated SharePoint-based system made it easier to manage workflows that track critical manufacturing events. It streamlined the manufacturer’s processes and provided a system that was more user-friendly, with greater flexibility and functionality. The system also provided an infrastructure for future expandability – functionality that wasn’t even considered in the past due to limitations of a paper-based system is now possible with an automated system.
More than a replacement
Now that it’s in place, the new SharePoint-based system provides a wide range of other benefits to the company, including:
• Automatically notifying proper personnel of an event based on alerts established in the workflow. For example, the Quality Manager can be emailed automatically once a significant quality event is detected.
• Requiring standard, step-by-step procedures be followed for every type of incident. If there is, for example, a quality event, it may require strict adherence to the established procedures and a record that the steps were completed, along with time stamp and names of those who completed each step.
• Checking to see if an incident is a repeat occurrence so that personnel can investigate why previous corrective actions did not solve the problem. The previous paper system required a time-consuming, manual review of the paperwork. An alert can now be configured to pop up anytime the same downtime event causes a specific amount of downtime within a certain period
An opportunity to improve workflows company-wide.
In addition to these benefits, the system can be rolled out to other manufacturing sites, providing the company with a re-usable system based on their current best practices. Corporate-wide visibility now becomes possible, since all of the manufacturing sites have adopted the same automated workflows..
How could you use SharePoint to collaborate across your plant?
Workflows exist in all aspects of a business. The processes you follow – whether in accounting, logistics, quality, maintenance or operations – can all be automated to provide consistency and accuracy. Just give us a call to learn some best practices for implementing automated workflow in your day-to-day life and make a difference to your productivity.
About Polytron
Polytron helps customers engineer and operate with manufacturing excellence. The company is based in Duluth, Georgia (north of Atlanta), applying its project management and engineering expertise in hundreds of engagements with many of the world's largest Food, Beverage, Pharmaceutical, and Consumer Products companies, as well as in the Water and Waste Water Treatment industries since its founding in 1983.
###
If you’d like more information about this topic, please call Brent Stromwall at (678) 328-2955 or email him at bstromwall@polytron.com.
www.polytron.com