Kaiser Permanente Lab Increases Efficiencies With Fastpic Inventory Management Software
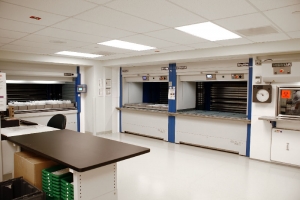
Kaiser Permanente Lab Increases Efficiencies With Fastpic Inventory Management Software
When Kaiser Permanente’s Mid-Atlantic region decided to consolidate its regional testing laboratory operations, management looked at different inventory management solutions for storing specimens, biopsy slides, tissue blocks, reagents and laboratory supplies.
Kaiser Permanente is the largest integrated health care and health maintenance organization in the U.S., serving some 8.2 million members per year. The Mid-Atlantic Region, the fourth largest of the eight geographic regions served by the organization in the U.S., handles medical testing for members located in Baltimore; Washington, D.C.; southern Maryland and northern Virginia.
It’s a very large operation, and prior to the consolidation, regional testing was conducted in four separate facilities. Because operations were dispersed, so was inventory management. There was duplication in ordering supplies, and, since storage and retrieval of all items was done manually, there were times when items were stored incorrectly. Inventory was stored on a traditional rack and shelving system and inventory was managed manually.
“Prior to the consolidation, we established a labor/management partnership group that identified areas where we could improve the efficiency of our operations,” said Ms. Lewis. “Since we operated out of multiple facilities, we found a lot of duplicated effort in ordering, storing and retrieving items, plus we found that our higher paid technical staff, responsible for performing medical testing, was often spending time away from that job to place orders.”
Kaiser Permanente integrated three Kardex Remstar Shuttle Vertical Lift Modules (VLMs) in the laboratory to store supplies such as gloves, masks and lab coats. A refrigerated Kardex Remstar vertical carousel was also installed to store reagents used in testing operations at an optimum temperature. All inventory is managed by FastPic inventory management and control software to manage inventory in the new laboratory.
The labor/management partnership at the Kaiser Permanente laboratory created a support services group that combined the skills necessary to support the technical staff in their daily testing procedures while adding to the overall efficiency of the operation. Combined with the FastPic inventory management software, this change has helped the laboratory realize significant productivity and materials utilization efficiencies.
“In the past, we’d have four different locations ordering lab coats, for example, and we always had more than we needed,” Ms. Lewis said. “Because we were manually restocking shelves, we would have particular difficulty with stat (emergency) orders. Our supply of a specific item might run out, and we would be unable to fill the order when needed, then we would over-order the same item to assure than we didn’t run out again. It was an inefficient method of stocking supplies,” she said.
The laboratory also experienced some difficulty with rotating stored items. Occasionally, using the former system, some stored items were not retrieved until after their expiration date. By law, dated materials used in testing operations must be used prior to their expiration date or they must be discarded.
“The installation of the Kardex Remstar automated vertical storage and retrieval systems, together with FastPic inventory management software, solved those problems for us,” said Erwin J. Cabling, Materials Coordinator. “Now, we don’t need to rotate stock. The software directs the vertical storage and retrieval systems to the location of the earliest to expire item and pick lights direct the technician to the specific item.”
The FastPic inventory mangement system has reduced the number of supplies contained in the laboratory’s inventory, as well. The technical staff keeps a week’s worth of supplies near their workbenches. Once per week, the staff provides a list of needed supplies to the materials coordinator who fills the order within 24 hours.
“The FastPic software lets us establish par levels of items so that we don’t have to keep track of each individual item in the system,” said Mr. Cabling. “We produce a reorder report once per week. We know exactly how much or how many of specific items we have remaining, and what we need to reorder using the software’s cycle count reporting feature.”
Mr. Cabling also receives a software generated expiration date report that indicates items set to expire in 30, 60 and 90 days. “Using this report, I’m able to order ahead of time those items due to expire first, and this saves money and time,” he said.
Restocking the system is simple. Employees tell the system, through the software, what they’re restocking and the automated system retrieves the proper shelf location for that item. In the case of a new lot that has a new expiration number, the system will present a different shelf for storage or the item. That way, materials are always used prior to their expiration date.
“Another system report that I can access on an as-needed basis is the summary of activity by part and date,” said Mr. Cabling. “With this report I can determine who retrieved a particular part how often. Based on this information, I can determine if specific items are being used more frequently and follow up with the person retrieving the items to find out why additional quantities are necessary. If necessary, I can instruct the system to order additional quantities of those items.”
In addition to improved inventory control and management, manpower productivity has improved as well. “Previously, we had six technicians each spending one and a half hours per week ordering supplies. Now, using the Kardex Remstar storage system with the FastPic inventory management software, we have one logistics specialist spending about four hours per week ordering and restocking the system,” said Ms. Lewis. This has resulted in a 56% improvement in productivity.