Ewon Provides Remote Service For High Precision Food Packaging Machines
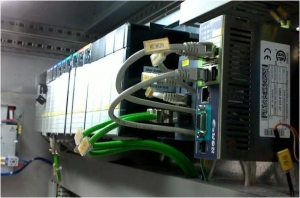
Ewon Provides Remote Service For High Precision Food Packaging Machines
A Rockwell Automation OEM customer, manufacturing and installing food packaging machines worldwide, uses eWON to perform customer support tasks from remote, across Internet.
Controlling plants remotely and doing maintenance from a distance has quickly become a necessity. Zacmi selected eWON’s Talk2M Pro service, in combination with eWON 2005CD hardware modules for its remote access needs.
Background
Zanichelli Meccanica (Zacmi) was founded in 1954 in Parma, Italy by Giuseppe Zanichelli and is still family-owned. The company designs and builds machines and complete plants for the food industry. Over the last few decades Zacmi specialized in line fi lling and closing installations for food products, non-food products and beverages. The company also manufactures machines that are capable of accurate dosing. This was considered as very challenging in the past, or even impossible, mostly
because of the very high accuracy often specifi ed in such applications. Zacmi also builds and delivers complete processing plants, especially for pasteurisation and sterilisation of food products prior to packaging, or for pasteurisation treatment of products which are already boxed in fl exible containers, tins or bottles. In addition, Zacmi’s business includes fruit and vegetable product transformation plants. Production monitoring through the internet is an ideal, low-cost and fast solution.
Challenge
”Over the years [the complexity of ] these programmable components have increased exponentially and the potential problems that can arise during commissioning have also increased proportionally” stated Mr. Andrea Scrivani, Industrial Automation Manger, Zacmi. “In the past the procedure required an engineer to be sent out to fix the problems or faults in the plant, often with very long
transfer times, even for simple and brief operations.” “Working with our distributor, we developed a remote connectivity project to allow PLC remote support for the plants. Our goal is to be able, in the next few years, to have a connection that allows us to address small problems, which may arise in the systems or remain after commissioning and start-up, without having to send programmers in support.
Solution
Since adopting the Talk2M & eWON solution, intervention times have decreased signifi cantly. Access via the internet allows the engineer to be virtually projected onsite, where the machine with the fault is installed, and, even though the communication speed also depends on the remote site’s infrastructure, the operation is undoubtedly quicker.” The selection of eWON came after clear operational needs which the product proposed by the distributor fully met: “We discovered eWON products at a trade show and we were impressed, fi rst and foremost, by the ease of installation of eWON, which is, so to say, basically automatic or at any rate very easy and requires just a few steps. Also, once a confi guration is defi ned and the expectations from the instrument are established, the system is extremely reliable. The third factor which infl uenced our choice was the excellent quality/price ratio, just perfect for our needs,” according to Scrivani. Another fundamental characteristic of eWON is its complete compatibility: because it is not exclusively tied to any product, a communication interface can be created with any plant or component.
Scrivani points out: “eWON, being compatible with any manufacturer, allowed us in particular to take advantage of the potential of Rockwell Automation products used in various applications.” In fact, as a standard, Zacmi uses a range of Allen-Bradley products from Rockwell Automation (PAC ControlLogix®, PAC CompactLogix™, PanelView™ Plus CE, Switch Inverter, Kinetix® 6K for motion control) in manufacturing the machines to be shipped to many geographical areas.
Results
The Talk2M Pro service was chosen after a careful analysis of the architecture requirements, in order to provide a support service from remote. “Initially we had thought about managing the system server and software ourselves completely, but that turned out to be a way too demanding project,” says Scrivani. “When, a structure like the one that Talk2M off ers allows us to guarantee service
interventions, in the event of faults, very quickly, at any moment or any time of day, by connecting to the machine network from any computer even when the company is closed.”
Fruitful Joint Collaboration with Rockwell Automation Encompass Partner eWON and Distributor
Last, but not least, Scrivani recalls how the selection of eWON products was also infl uenced by the relationship with the distributor. “Our local distributor supported us and guided us from the beginning in a very careful and consistent way. We always had quick and effi cient answers
to our requests and expectations, to the point that we are thinking of expanding our cooperation to
other applications.”