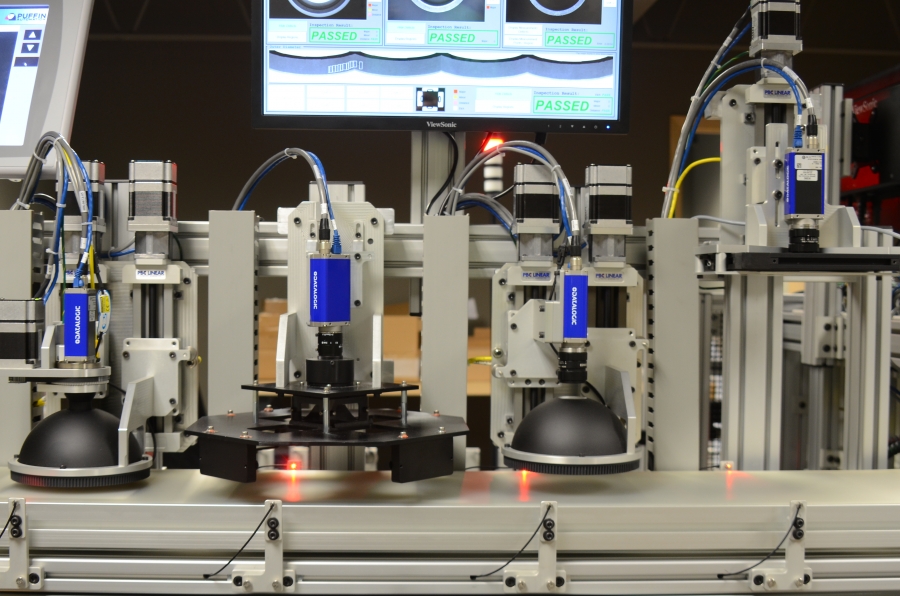
Engine Ring Inspection System
Automatic Vision Inspection Configuration for up to 1500 Part Variations.
Custom Machine Vision solution for detecting surface defects on metal alloy engine rings.
Because of increasing demand for their products a manufacturer of automotive engine ring parts needed to upgrade their existing inspection technologies to meet the higher production demands. The system had to be capable of inspecting up to 1500 part variations. Along with the large variation of parts there is a need for the parts to be inspected for tiny defects on all surfaces and for accurate repeatability in that inspection. Material handling and change over can also be expensive and complicated with such large part variations.
Puffin Automation of Eden Prairie, MN (www.puffinautomation.com ) was tasked with creating a system that would inspect an engine ring on all four surfaces, have a changeover of less than 1 minute with repeatability in inspection, inspect 1500 individual part numbers varying from 1 to 3 inches in diameter and .125 to .75 inches in height, and still be easy to operate. Such a system was developed through an in-depth study of the requirements and a close working relationship with the customer.
The system needed to be designed around the vision component with attention given to material handling. Some serious challenges were faced in designing a system that can handle the large variation of parts and still have the capability to inspect all surfaces. Previously the customer had used linescan cameras to inspect the inner and outer surfaces of the part. This approach while ideal from a machine vision standpoint due to the lighting geometry achieved with this style of system, but it quickly becomes complex when material handling is considered. Previously the parts were rotated in front of the linescan cameras using large dials and robots which became costly to set up and maintain.
In the development of the new system the breakthrough came with the implementation of Datalogic’s IMPACT hardware and software, creative optical solutions, proper illumination of the defects, a central recipe control managed by a Rockwell Automation PLC.
This solution consists of two conveyors with clear belting and a flip-over device between them. The clear belts allow for backlight illumination to be used and flipping each part allows for all surface to be inspected with a frame acquire camera. The conveyor system is a simple and cost effective way to move parts downstream in the inspection system while still maintaining proper illumination. A simple part alignment device was utilized at the beginning of each conveyor to properly center the part under the cameras.
Six inspection stations incorporating two Datalogic (www.datalogic.com ) M-Series industrial processors and 6 M-series cameras where utilized. Ultimately only 4 stations are needed to check 4 surfaces, but due to the customer’s variation in part geometry, two inner surface inspections were utilized. A sixth station was then added due to specific light geometry that was needed to inspect for concentricity defects on the top face of the part. The order of stations is as follows: inner surface (part orientated up), outer surface, top surface, concentricity (part orientation is then reversed), Inner surface (part orientated down), and lastly bottom surface. To compensate for the variation in part dimension all cameras and lighting were all mounted on linear stages and controlled by the PLC recipe management for each individual part.
Besides the challenges of illumination of the parts, the inner and outer diameters proved uniquely challenging when using a frame acquire camera due to the surface orientation to the camera. The identification of defects in the inner surface was accomplished by utilizing an Opto-Engineering (www.opto-engineering.com) hole inspect lens. This lens has an extreme wide angle of view and is capable of inspecting the inner surface for casting defects. The difficulty with using this lens on variance of sizes of parts is that the lens will need to be focused. Moving the camera up and down may focus the lens at a certain distance from the end of the lens, but if the lens can focused at a set distance by the operator the part can be as large in the field of view as desired and still in focus. Since this lens does not have a manual focus a belt driven focusing device was created for these stations to thread the lens in or out of the camera body.
On the Outer surface station a linescan camera would have been ideal, but it added rotation motion into the system and part handling that would be expensive. To overcome this an optical splitter assembly created four overlapping images of the outer surface of the part and the power of Datalogic’s IMPACT software was to used to stitch(these images together and then inspect the stitched image. Stitching of the image was necessary to achieve proper classifications of defects.
After these complexities were ironed out the remaining problems needed to be worked out programmatically. To solve the problem of keeping track of the data for each individual part a Rockwell Automation PLC running a recipe management program that can store up to 1500 part recipes was utilized. All of the data from the linear stages, vision processors, and other part specific parameters are stored in a recipe in the PLC. The PLC has the ability to send the recipe data out to all of the components in the system via Ethernet IP when a recipe is downloaded by an operator. This capability allowed for rapid changeover times of approximately 30 seconds when switching to a stored recipe where previously hours were wasted.
Other vision systems utilize this same concept of data management, but the recipe is stored and processed by the vision device. This has its limitations. The amount of recipes you can hold is limited to the memory of the limitation of your device and loading and unloading files can sometimes take long amounts of time if the vision program file gets large enough. To combat this problem, the vision devices on this system were programmed with a central recipe task that has “data instances” that hold the information from the PLC tags. This task is consistently being written over and the vision system reacts based on the information store here. The vision device itself will overwrite this data if an operator is interacting with one of the Vision HMIs and changing parameters. This data is immediately sent to the PLC and can be easily saved by an operator.
The inspection system has three HMIs to interact with which may seem daunting at first, but they have been programmed with the operator in mind. The main system HMI is the system’s Rockwell PanelView monitor. From this HMI all other interactions take place including the navigation of the system’s 2 other Vision HMIs. In this way there is only one password login, one setup button, and single run button. Based on the user’s interaction with the AB Panel View the PLC sends information to the vision system which will auto navigate to the correct screen for the user. This drastically simplifies the control of system. When a station is selected for new recipe creation or editing of a current file an individual setup screen for the station will be navigated to automatically so the recipe parameters can be entered. Integration like this is possible through the use of Datalogic’s IMPACT Suite software that enables a user to create vision inspection files and custom vision HMIs. This software enables an average vision user to make a truly one of a kind solution.