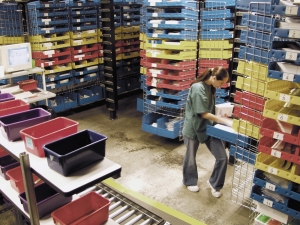
Advanced Picking Techniques Pay For Themselves
When it comes to improving the picking process for /operationkeyword/ organizations, accuracy & efficiency are two major components. By applying picking strategies such as pick and pass, parallel picking and batch picking techniques, companies are able to increase throughput up to 500% over manual systems and reduce capital acquisition costs by decreasing labor needs and utilizing less floor space.
The need for understanding an organizations business plan, objectives and financial realities are required to determine the best integrated solution and picking strategy. There are three key techniques that can be implemented. Pick & pass, parallel picking and batch picking processes can be applied to almost any facility by determining the equipment needed for each picking zone, the available floor space and return on investment.
The pick and pass process is primarily used for an order profile which averages one or two totes per order. Individual items for a specific order are picked at one workstation and put into a tote. The order/tote is then passed to the next workstation where additional items for the order are picked and placed in the same tote. At the end of the line, the complete order is ready for shipment. Pick and pass can eliminate costly lanes of conventional consolidation conveyor and reduces floor space needed. Using automation for pick and pass can save /industrykeyword/ companies up to 66% in labor costs.
Parallel picking is a methodology that can be used in medium to large /applicationkeyword/ distribution applications and is most beneficial to multiple zone picking operations. It is a process in which a wave of orders is released for picking to each individual work zone. An operator in each zone picks their designated items simultaneously and transports them to the consolidation area. This allows each zone to work efficiently and increased turn around time. Each pick zone can use the best of breed material handling solutions for its inventory profile. Fast, medium or slow movers can have equipment, labor and velocity balanced to meet facility business demands, saving costs.
Batch picking is the process of picking multiple orders simultaneously to achieve greater efficiencies. This operation increases efficiencies in labor since an operator will touch an inventory location once for the batch being picked, reducing the time required to pick each item. Batch picking can increase throughput up to 500% when compared to manually picking single orders.
The picking methodologies incorporates manual and automated equipment into one dynamic system allowing /operationkeyword/ organizations to reduce capital acquisition costs and increase overall productivity levels. Facilities can match "best of breed" equipment to efficiently utilize horizontal carousels, vertical lift modules and pick–to-light systems to accommodate fast, medium and slow moving parts.
KardexRemstar Inc., a company of the Kardex AG Group is a leading provider of automated storage and retrieval systems for manufacturing, distribution, warehousing, office and institutions. For information about KardexRemstar picking techniques, call 800-639-5805 or visit the KardexRemstar web site at www.KardexRemstar.com.